Industry Knowledge
At Sustech we believe in sharing engineering knowledge that originates from the scientific principles. We love co-operation through the knowledge-sharing. Anybody, who has dared to run small/medium business should be able to run it efficiently and focus on the core of the services they provide and not on the myriads of chores, could benefit from the knowledge leading to business intelligence. This could potentially improve overall business-efficiency in the small/medium business sector, with tangible benefit to employee wellness and a healthier workplace.
Story of a Leaking Heat Exchanger
Stories of leaking heat exchangers arise in old plants like ghost stories in abandoned houses. But this story is worth telling because it happened in a new plant. This is a story of engineering behind the scenes.
In the beginning …
It was a fairly new gas plant. But, the Amine Plate Heat Exchanger started leaking, causing the plates to corrode. The plant was shutdown. The plates were cleaned. The gaskets were changed. The plant was started again. Within months the heat exchanger started to leak again. The tiresome and expensive process of shutting down, cleaning, changing was repeated. The plant was restarted once more, only to shut down once again. Each shutdown cost the operator millions of dollars. The operator contacted the vendor demanding a resolution to the issue caused by the malfunctioning heat exchanger. The vendor said that they were not at fault. That model of heat exchanger has been around for a while, used widely and no one else was facing a problem.
-
We got a call
The operators were wise. They took the sensible option of engaging independent third party engineers. As independent third party engineers, our focus was mostly on looking into the defects of the plate heat exchanger and to proceed to FEA if needed to simulate and prove those defects. Time was of the essence as we were engaged during the 4th shutdown. A quick solution was needed to stop the recurrence of leaking incidents and loss of revenue.
We went to have a look
We visited the site to examine the heat exchanger and the condition of the plates and gaskets. We collected first-hand information and looked at the process of running the plant as a whole.
We found that the Plate HX was dismantled, the plates were corroded and the gaskets were torn
Installation MDR was showing that everything was in order
The maintenance log was showing right torqueing of the heat exchanger bolt
The exchanger plates were made from stainless steel and the gaskets were made of rubber as per the MDR
No significant pressure or temperature spikes or excess flow condition was noted in the operation log
We gathered, after interviewing operators, that the leaks start within a few days of startup and the quantity continues to increase as the days go by
The gaskets were replaced to the specification of the OEM. A few plates were also changed to the OEM specification
We walked the line armed with the piping layout in our hands and discovered that the first support of the pipes in front of the heat exchanger was restrained on all sides. This looked a little suspicious.
Our Reasoning
We thought long and hard about what we found. We came to these conclusions:
The heat exchanger selected and installed as per API 662 was fit for the purpose from the process point of view
The materials used were certified as per EN10204
The process data showed that there was no flow induced forces
So, we thought, the problem must be with the piping. The pipe stress analysis as per ASME B31.3 for the piping configuration showed induced forces and moments on the heat exchanger nozzles. These loads were being transmitted in its entirety to the HX body, thereby distorting and compromising its integrity. The liquid was finding its capillary path through the gaskets, corroding the faces not designed for exposure. The liquid was eventually making its way out through the HX plates’ path.
Restraining the pipes on the axial direction, was inducing loads beyond the allowable limits of HX nozzles
Why was this? Well, the earlier stress analysis did not get the confirmation for the loads from the HX vendor
Our Solution
We provided the following solutions to ensure a fully functioning, hassle-free plant:
Remove the guides on the pipe supports in the axial direction to the heat exchanger nozzle from all first supports in front of the HX
Provide a Teflon pad under the pipe support fixed with a counter sunk screw to the base plate on the steel member
Put a position mark for the pad to monitor the pipe movement. Keep regular vigil on the condition of the Teflon pad
Modify a few support locations and type of supports at the heat exchanger and air cooler end to satisfy allowable nozzle requirements of the equipment as per API 662 standards.
A Happy Ending
In short, the story had a happy ending. We helped reduce unplanned shutdown hours. The availability of the plant was increased due to our investigative and consultancy work. The owner was saved millions of dollars. We were happy to help.
Solution to Blown-out Steam Header
A long time ago an accident occurred at a steel plant powerhouse. The turbine lead steam header of a LP back pressure type steam turbine had blown off from one end, releasing steam under pressure. We heard that two of the plant’s operators died and more were injured. We were called in to investigate.
The initial finding by the owner’s engineer revealed that after 30 years of operation, there was a shear failure at the welding between the header and the endplate. We were not fully satisfied that this was the core reason for the failure. We decided to delve in deeper.
-
Gathering Evidence
To begin with, we collected drawings of the piping and the building. We asked for the MDR, operations data and maintenance data, but none was available. However we did get an important piece of information from the plant operators, who told us that they had heard hammering noises in the turbine lead header. But besides that we had to rely on our first-hand observations, which were:
The curved endplate was made of the same material as the pipe (DN250 ASTM A106 Gr.B)
Shearing was from the welding line
Insulation was tattered in some places allowing heat transfer to the atmosphere
There was no steam trap drain line to take the condensate away from the main line
The piping was spring supported throughout, but one of the springs at the top, near the safety valves was locked – maybe in order to prevent the line from vibrating
Analysing Evidence
It was clear that the welding had given way. But, it is important to note that the welding and the endplate survived for 30 years. So, the root of the problem must have been deeper. It seemed to be something to do with the high pressure. Surprisingly the endplate was cut from a similar pipe to the header. This was a non-compliant use of material and the thickness of the cut pipe was less than that was needed for an end plate under ASME B31.1 for a design condition of 2000 kPa at 215° C.
Although hard to prove in the absence of process data, it seemed that the hammering sound indicated the presence of saturated steam and condensate in the line, possibly creating a steam hammer. The condensate was being formed due to the tattered insulation, which was causing heat loss. We found through pipe stress analysis that the lowest point of the line, due to thermal movement, was near a spring, which was bottomed out. The locked spring support, acting as a vertical rigid one, near the safety valves, was causing the piping to grow all the way downwards as it expanded with heat. This was bending the elbow so far that the condensate began to collect in a pool, restricting the flow of steam, causing a hammering noise. One day, when there was too much condensate, the steam escaped by blasting through the weakest point in the line – the endplate.
Providing Solutions
Our tehnical solutions were:
Replace the end spool of the turbine lead header with a new pipe and a BW cap
Repair and provide proper insulation
Provide steam traps and drains at the lowest points, determined by pipe stress analysis under operating conditions
Move the location of the safety valves
Provide spring support at the first support on the roof top
Modify support locations and change some of the springs
Do non-destructive tests of new joints and old ones
But our solution did not stop at the design-installation. The incident was also clearly preventable through proper maintenance and good organisational practices. So, we advised the owners to:
Maintain operations process data, keep a maintenance log
Establish an early reporting protocol of any deviation in process parameters or anomalies observed by the operators
Engage owners’ engineering specialists for any modification and organise third party review at regular intervals for health check
Averting Failure
There were a lot of lessons to be learnt in failure aversion from the endplate incident at every stage of the project. We have summarised a few underneath from each phase.
Project Management
Close and conservative material management
Design Phase
Proper design and analysis considering all failure modes
Appropriate design foresight
Using standard components design as much as possible (do not deviate under duress)
Executions Phase
A construction contractor should follow design more closely
The quality inspectors should be more thorough
Commissioning
Checking Design Review and other safety review reports and ticking off all punch list items to satisfaction
A proper review of MDR
Operations Phase
Early heads up
Operators need to have more detailed knowledge of handled fluid
Retain and analyse operations & maintenance data
Proper maintenance regime
No modification without designer’s consent
The methodology of doing a project has been established over hundreds of years. The process is tedious but needs to be followed meticulously. Any shortcut or variation unapproved by the design group can spell catastrophe, if not now, then in the future.
100 years of the BPVC code
“A Century of Safety” – The title of the ASME article celebrating the centenary of the BPVC (Boiler and Pressure Vessel Code). The BPVC is the mother of all American codes. The existence of this code and its derivatives mean that the engineering industry is a much safer place. Perhaps we should take some time to thank the people who made and contributed to the codes. These are people, famous as well as ordinary, who have charted the territory which we as engineers of today can confidently navigate. We are greatly indebted to these forefathers of our profession and hats off to people behind BPVC and all other engineering codes around the world, like our own AS2885 or the international ISO14692, ASME B31.1, B31.3, B31.8 and many others.
-
Here are a few lines from the article published by ASME that will give you a bit of taste of history:
“When ASME’s founders—including Henry R. Worthington, Alexander Lyman Holley and John Edson Sweet, along with other prominent industrialists and technical innovators of the nineteenth century— gathered in New York City for the first time in 1880, the main topic of discussion centred on the need for standardized tools and machine parts as well as uniform work practices in the dawning industrial age. Engineering standards, the founders agreed, would ensure safety, reliability and operational efficiency in machine design and mechanical production.
ASME issued its first standard, Code for the Conduct of Trials of Steam Boilers, in 1884. This paper evolved into Rules for the Construction of Stationary Boilers and for Allowable Working Pressure—the first edition of ASME’s now-legendary Boiler and Pressure Vessel Code (BPVC)—issued in 1914 and published in 1915.”
It has been a long way since. By far the BPVC has done its job right in standardising designs, building safety into design, preventing the loss of lives and harm to environment and property.
But what exactly is a code? Put simply, it is a book where all the collective engineering experience and knowledge is compiled to “ensure safety, reliability and operational efficiency.” But a book is useful only as long as it is read. So the legislation has instilled regulation and our profession implements those through internal review, peer review, safety in design review, HAZOP, independent third party review, design verification, MDR validation and code compliance. When these processes are followed diligently with the assistance of the right people, the result is a much safer and productive installation, low on maintenance and high on availability, therefore high on profitability.
There was a popular phrase till a few decades ago: There is no royal road to education. Similarly there is no short cut to safety. Given the scale of industrialisation that has happened throughout the world, and the new heights that technology has scaled we know that we have achieved greater safety standards than hundred years before. But the goal of zero harm is yet to be reached.
We have heard of Chernobyl, 3 mile Island, Deep water horizon, Fukushima Daichi, Varanus Island and Pike River. The memories of these incidents make us think and rethink our role as engineers. Every time an industrial incident happens anywhere in the world, as engineers we ask, why did this happen? Could this have been averted? What can we do to prevent accidents like this in the future? Then when we get the opportunity to do a root cause analysis, we use the same process of questioning to find the cause to prevent future recurrence. That’s our duty of care. From my experience of two decades of engineering, the lesson I learnt is to abide by the code to make a safe and efficient installation. I learnt to enhance and bring clarification to the code and to raise awareness about codes such as the BPVC and their purpose to make societies and communities safer.
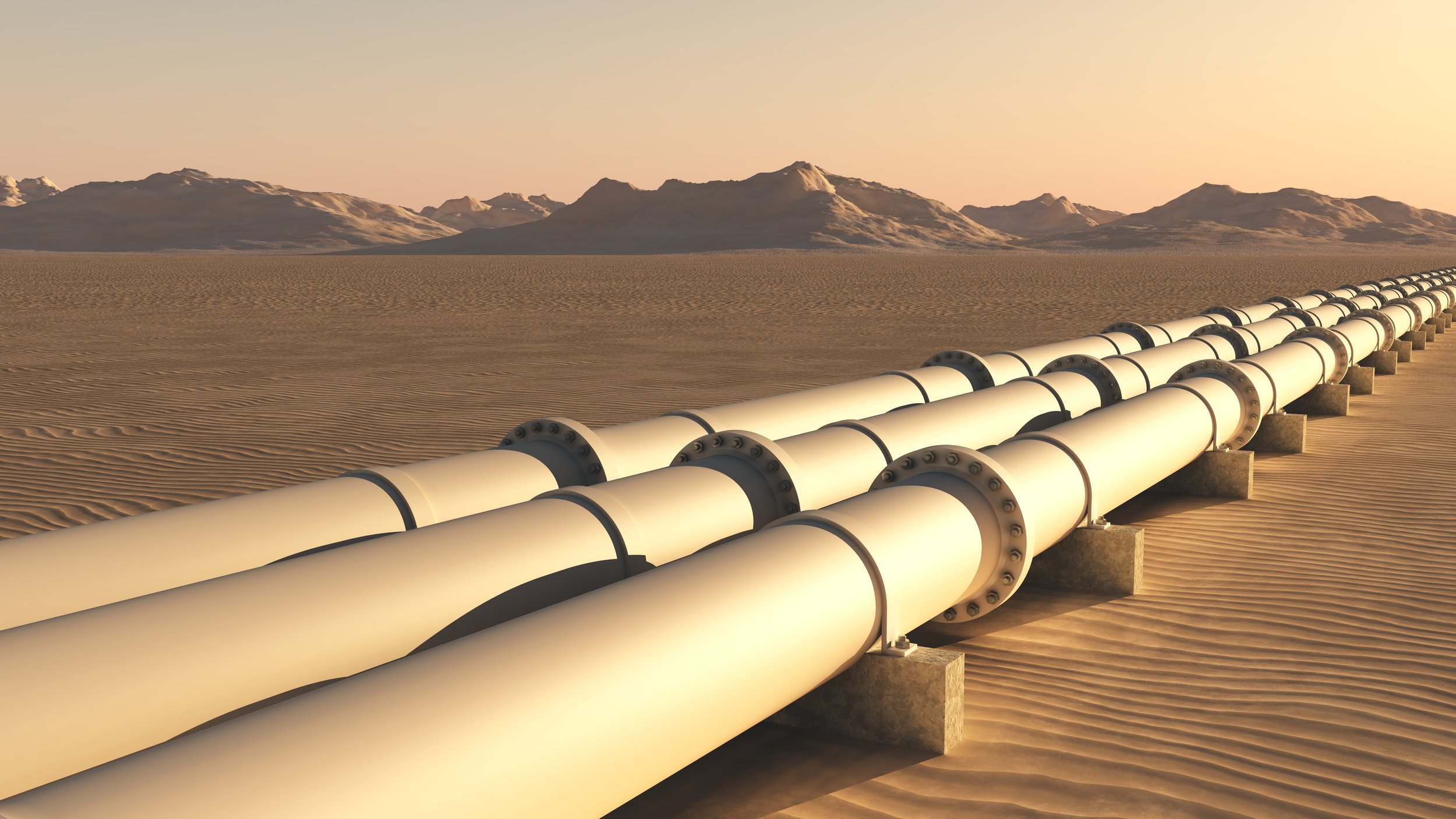
Role of pipelines in climate change
GLOBSYN Management Journal
GLOBSYN Management Journal
The opportunities and problems of small engineering consultancy business in Australia in post Covid-19
AI & Energy: Challenges and Prospects
Impact of AI on Energy and Ethics